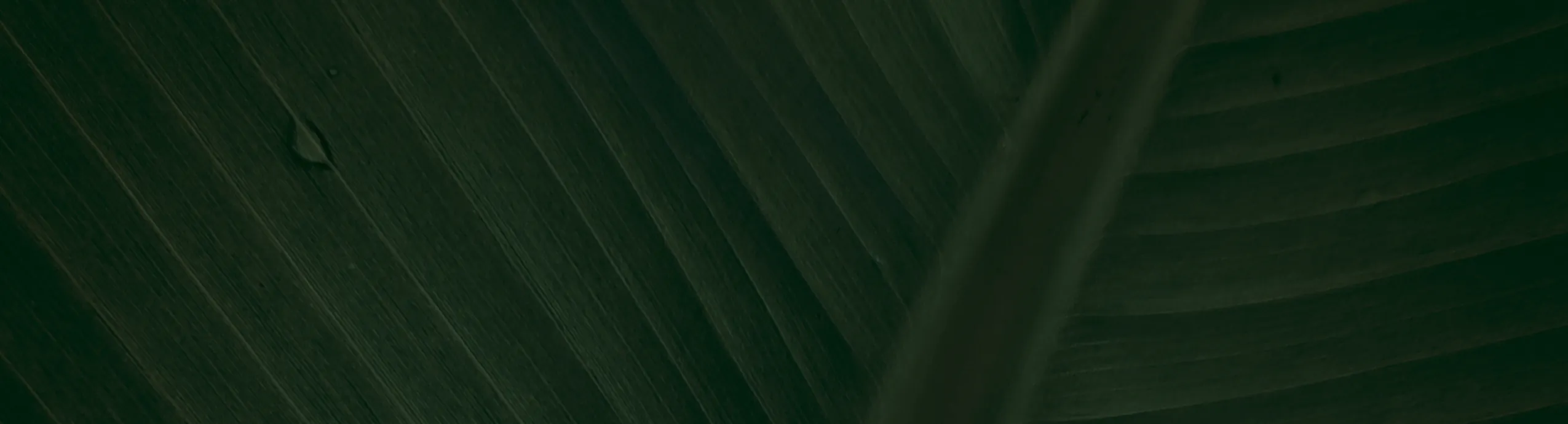
Dokra Metal Craft
Dokra (also spelt Dhokra) is an Indian Heritage Craft known for casting of non-ferrous metals (mainly Brass and Bell Metal). It originated in India over 4,000 years ago. Lost-wax casting technique used in producing Dokra artefacts is one of the oldest enduring metalwork methods on Earth. Dokra is a skilled craft form producing objet d’art. Dokra aka Dhokra artefacts are in demand in India as well as many foreign markets because of their enchanting simplicity, captivating primitive folk themes, ideas and forceful form.
Dokra artisans create small, delicate artefacts, such as figurines (human, animal or divine), jewelry, lucky charms and utensils. These artefacts often carry intricate patterns of which many are finished in beautiful colors. One of the earliest known lost-wax artefacts is the ‘Dancing Girl of Mohenjo-daro’.
The most popular Dokra products comprise Tortoises, elephants, horses, owls, peacocks, religious images, tribal figurine, lamps etc. Thereafter the figurines get diversified forms such as pen stands, cutlery holders, candlestands, utility boxes, other decorative or utility items and much more. Most of the themes revolve around local beliefs, religion and Indian mythology with many variations seeping in over the centuries.
The lost-wax casting technique is eponymic to Dokra Damar tribes, the main traditional metalsmiths which initially resided in Bankura-Dariapur belt in West Bengal, parts of Odisha, Chhattisgarh and Madhya Pradesh. Despite different locations and difference in language this tribe extends from Jharkhand to West Bengal and Odisha. The members of the tribe, over the centuries, have moved to southern and western parts of the country, thus presently covering large parts of the country.
Key features of Dokra art because of which there is increasing demand for these products.
• The oldest surviving metalcraft process – the lost-wax casting technique.
• The historical and cultural significance of this art form.
• Delicately handcrafted patterns, forms and colors.
• Victory of man over machines in terms of design intricacies.
• Longevity of the artefacts.
• All natural materials.
Lost-wax technique – A wax model of the desired object is painstakingly crafted. The wax model is then covered in a clay shell, and the clay shell is baked. The wax melts and runs out of the clay shell, leaving a hollow space. The clay shell is then filled with molten metal, and the metal cools and hardens to form the final object.
Lost-wax casting technique comprises two main types based on the process followed: Hollow Casting and Solid Casting. While Hollow Casting is more common in Central and Eastern India, Solid Casting is predominant in the south of India. Hollow casting is the more traditional method which uses a clay (usually riverbed clay) core. Artisans in some areas, away from rivers, replace clay with a mixture of local soil, coal dust and rice husk. Solid casting, on the other hand, uses a solid piece of wax for the mold.
The first step in the Hollow Casting process is to craft a clay core made in the shape of the final cast output product. Thereafter this core is covered with thick layer of pure beeswax mixed with saps and resins from specific local trees. This wax layer is carved with desired patterns designs, designs and decorations in their finer details. This leads to the third step of covering this assembly with layers of malleable clay which takes the reverse form of the designs on the wax. This makes for the final mold for the artefact. Molten metal is poured into this mold. The wax melts, drains away, leaving desired space for the metal to fill. Once the metal solidifies and cools inside the mold, the outer layer of clay is scrapped off to get the final product. Polishing and finishing, as may be required, follows and the product is ready.